With the increasing global focus on reducing reliance on fossil fuels, automotive companies are investing heavily in hybrid and electric vehicle (EV) production. These companies are pushing the boundaries of battery technology to achieve longer mileage range, faster charging, and better efficiency. While fully electric vehicles may grab most of the headlines, hybrid sales, including plug-ins, have been booming over the past few years. As a result, car manufacturers are struggling to keep up with the current EV demand, especially when it comes to battery production. This post will delve into recent breakthroughs in battery technology, showcasing what the future of automotive industry could look like.
Scientific breakthroughs are not always about "creating a new battery chemistry" or "inventing an engine that runs on household waste." Sometimes, significant progress is made by improving existing concepts or ideas. Tesla and Panasonic, for example, are currently working on mass-producing their 4680 battery cells. This type of battery is larger and heavier, packing more power and energy into each cell. This format also reduces the excess material and lowers the overall cost per kWh. However, Tesla has encountered issues with performance and production, and is seeking assistance from material producers and battery companies like LG and Panasonic to overcome these problems.
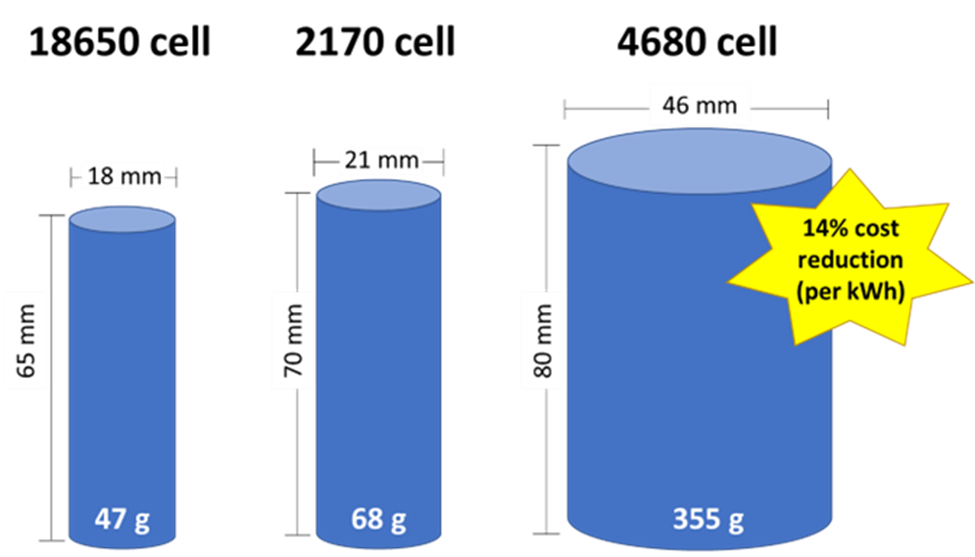
Two highly anticipated innovations in battery chemistry are solid-state batteries and sodium-ion batteries. Solid-state batteries use a solid electrolyte instead of a liquid one. A successful solid-state battery would improve energy density, reduce flammability, and last longer. The biggest hurdle is developing a stable, high-performance material for the electrolyte. QuantumScape, a company based in San Jose, CA, claims to have found a solution by using a ceramic-based separator that can transport lithium ions and prevent dendrite formation. Dendrites are needle-like structures that can form during charge cycles and potentially short-circuit the battery, leading to explosions or fires.
Sodium-ion batteries are being developed to address the growing demand and cost of lithium. Companies are searching for ways to increase the energy density and power of sodium-ion batteries and reduce reliance on the lithium supply, which is primarily controlled by China. Sodium-ion batteries also have a reduced risk of fire and better performance in cold temperatures.
In addition to these innovations, companies are exploring other solutions. Manufacturers have traditionally used nickel cobalt aluminum (NCA) or nickel manganese cobalt (NCM) as cathode materials due to their high energy density. However, companies are now considering using an older chemistry type, lithium iron phosphate (LFP), which offers cost savings and improved safety. Bloomberg projects that LFP batteries will grow substantially in the coming years, approaching 40% market share.
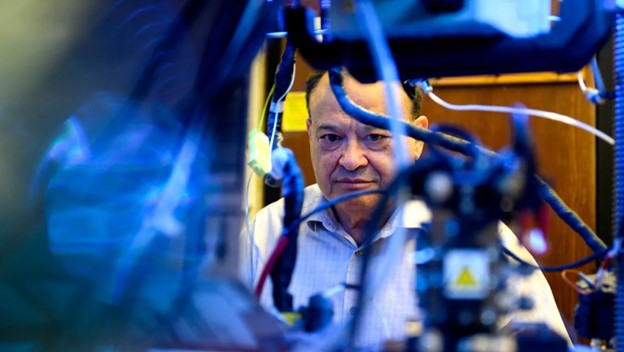
A more futuristic approach comes from a recent article published in Nature magazine, which reports on a superconductor that works at room temperature. Historically, superconductors could only carry electricity with zero resistance at extremely cold temperatures. However, by doping lutetium hydride with nitrogen at high pressures, the material reportedly maintained its superconductor properties up to 70 degrees F. This development could unlock longer-lasting batteries, among other applications.
Across all disciplines, whether in science, engineering, or manufacturing, companies are committed to providing better energy storage and conversion. For automakers, batteries are a crucial component of vehicle design and production. These recent developments show how the industry plans to address current problems by finding the balance between performance, charging speed, and battery lifespan. With continued innovation and investment, the future of battery technology looks bright, offering significant promise for the future of the automotive industry.
As companies race to develop new battery technologies, a critical question looms: what will happen to the millions of batteries that reach the end of their lifespan each year? At A3 Global, we're taking a proactive approach by focusing on the development of innovative techniques for repairing, reconditioning, refurbishing, and remanufacturing batteries - collectively known as the 4R process. Given that the Earth's natural resources are finite, it's becoming increasingly challenging to keep up with the demand for new batteries. Highlighting this point, at a recent Stellantis-hosted event, CEO Carlos Tavares remarked that there might not be enough lithium to replace every internal-combustion vehicle with an EV. By implementing the 4R process, A3 Global can solve this looming problem by reviving used batteries and reintegrate them into the circular economy, establishing a self-sustaining and eco-friendly system that promotes efficiency, reduces costs, and minimizes unnecessary waste.
Our flagship product, the NuVant EVc-30, reconditions nickel metal hydride batteries utilized in hybrid electric vehicles (HEVs). However, battery reconditioning is just one element of our comprehensive battery remanufacturing process. In the near future, we'll be launching the LVc-40, a diagnostic and repair tool for lithium-ion batteries. To stay the loop with how A3 Global is driving the future with sustainable mobility solutions that empower the circular economy, sign up for our monthly newsletter here.